Application of acidic accelerator for production of pure hydrogen from NaBH4
Authors
- Wameath S. Abdul-Majeed
- Muhammad T. Arslan
- William B. Zimmerman
Table of Contents
- Abstract
- Introduction
- Methods
-
Results And Discussion
- Fig. 2 Effect of NaBH4 concentrations on the hydrogen stream generation rate at different fuel solution flow rates and accelerator concentrations. HCl flow rates were 0.97 ml/min in case of 4 M and 1.25 ml/min in case of 3 M
- Fig. 3 Effect of NaBH4 concentration on the hydrogen generation efficiency. HCl flow rates were 0.97 ml/min in case of 4 M and 1.25 ml/min in case of 3 M. NaBH4 solution flow rates were 1.25 ml/ min in case of 4 M HCl and 0.97 ml/min in case of 3 M HCl
- Fig. 4 Estimated power output from PEM fuel cell at different concentrations of NaBH4 and HCl. HCl flow rates were 0.97 ml/min in case of 4 M and 1.25 ml/min in case of 3 M. NaBH4 solution flow rates were 1.25 ml/min in case of 4 M HCl and 0.97 ml/min in case of 3 M HCl
- Fig. 5 A chromatograph for a collected sample of generated hydrogen stream from 2nd GLS upon injecting 25 wt% NaBH4 and 3 M HCl at 0.97 and 1.25 ml/min, respectively
- Table 1 Experimental results—10 % NaBH4 and 3 M HCl
- Table 2 Experimental results—25 % NaBH4 and 4 M HCl
- Table 3 Experimental results––30 % NaBH4 and 3 M HCl
- Table 4 Sample of a GC analysis
- Conclusions
- References
License
Abstract
Feasibility of using hydrochloric acid (HCl) as an accelerator for onboard production of hydrogen from sodium borohydride (NaBH4) is investigated. The aim was to examine process efficiency, hydrogen purity and process controllability which concurs onboard 2015 hydrogen storage target (5.5 wt%) for vehicular fuel cell system application. Results showed that a highest yield and controllable hydrogen production rate are achievable upon adopting onboard reaction of HCl (3 M) and an aqueous alkaline solution of 30 % NaBH4 via a T-junction and applying a gas–liquid separation of two stages. Cost evaluation and product stream analysis have demonstrated an exceptional performance for the examined scheme and relevancy to be adopted for feeding vehicular electrochemical fuel cell systems.
Introduction
In view of the fact that hydrogen is the key energy carrier, interests are increasingly exhibited to utilize it as a fuel for internal combustion engines and electrochemical fuel cells. Nevertheless, technical issues such as storage and transportation are still big barriers against its wider use [1] .
Hydrogen can be stored physically as a compressed gas or in liquid form. Nonetheless, pressures required for compression are too high because of its low boiling and melting points. Thus, very few materials, so far, can handle this much pressure. Hence, compressed hydrogen is not user friendly due to the risk of leakage and explosion hazards, which limits its commercial availability worldwide [2] . On the other hand, fuels such as methanol, ethanol and methane can be a source of hydrogen. However, operational requirements (e.g. high temperature) are restricting its economic use for fuel cell applications [3] . Alternatively, hydrogen can be stored chemically in a solid state medium such as metal and chemical hydrides which are considered to have a great potential to store hydrogen effectively and safely under standard conditions [4] . Principally, chemical hydrides are more advantageous compared with metal hydrides in terms of hydrogen content, storage capacity and operational requirements [5] . As a safe onboard hydrogen storage candidate, sodium borohydride (NaBH 4 ) has gained the highest gravimetric/volumetric hydrogen storage capacity over other chemical hydrides (theoretically = 10.8 wt%) as well as other features such as nonflammable, non-toxic chemical and its stability in dry and alkaline conditions.
Although voluminous literatures showed a significance of applying solid state hydrogen generation system for vehicular portable applications, it has been given a No-Go recommendation by the US Department of Energy (DOE) due to several technical and economical issues. Reasons were reported to be mainly related to a difficulty in recycling meta-borates to borohydride and incapability to achieve system storage targets [6] .
Hydrogen can be generated from sodium borohydride through catalytic hydrolysis reaction at low temperature, in which four moles of hydrogen are released in addition to the sodium meta-borate as by-products [7, 8] .
Using sodium borohydride at 10-15 wt% was considered to be optimal by several researchers [9] , as it reacts very slowly with water. Therefore, it can be stopped readily by addition of alkaline medium (e.g. sodium hydroxide) or accelerated by adding acids or applying catalysts (e.g. metals of both noble and non-noble nature) [10] . Although a catalyst (e.g. RU) was reported to be able, theoretically, to provide up to 100,000 turnovers, nonetheless, practical issues such as onboard regeneration were found to be a big barrier against its industrial adaptation. Hence, higher hydrogen yield and conversion efficiency are better achieved when applying acid catalysts. This is due to the fact that all reacting species (H ? ) are completely consumed and therefore the hydrogen generation rate is controlled precisely through addition of acid, which is highly requested for onboard applications. The acidic scheme is illustrated by the following reaction [9, 10] .
Utilization of acid accelerators for NaBH 4 hydrogen generation system was first tested in 1950s, in which more than 20 acids were assessed (e.g. oxalic acid, citric acid, boric acid, formic acid and many others). The results showed that the reaction upon adding these acids was very violent and vigorous; hence it was decided to choose a relatively safer option [7] . Until beginning of 2000, acids were found unsuccessful accelerators for NaBH 4 hydrolysis due to safety issues. However, recent research endeavour showed that some acids can be used as potential direct accelerators or indirect activator for heterogeneous catalysts (Xu et al. 2008 and [11, 12] ). Moreover, there were few acids suggested by [13] which could be used as a single-use accelerator for a portable NaBH 4 hydrogen generation system. These acids include hydrochloric acid, sulphuric acid, nitric acid, phosphoric acid, formic acid and acetic acid. They also found that some acids possess the ability to delay formation of hydrated by-products, via shifting pH to lower values, and thereby NaBH 4 hydrolysis could be improved [3] .
Main advantages of the acidic hydrolysis scheme are: (1) acid accelerators can be stored as an aqueous solution of variable concentrations, (2) the scheme can be performed at room temperature, (3) sodium meta-borate produced was shown to be barely toxic and environmental friendly, which makes it possible to be recycled, (4) high purity hydrogen gas can be obtained, which suits highly sensitive fuel cells such as Proton Exchange Membrane Fuel Cell, (5) upon using acid accelerator, formation and crystallization of by-products is delayed or inhibited, and (6) Practically, even with 1:1 (HCl:NaBH 4 stoichiometric ratios), applying acidic scheme is believed to be costeffective option for onboard fuel cell applications, taking into consideration the operational troublesome for metal catalysts (e.g. Ruthenium, CoCl 2 ). Consequently, acid accelerators may act effectively for onboard fuel cell applications should a sophisticated scenario defines the optimal operating conditions becomes applicable.
It is worth noting that an acidic hydrolysis scheme was explored with less attention compared with catalytic schemes, therefore it is required to conduct further researches toward better system understanding and to measure feasibility for a portable fuel cell application.
In a previous work [14] , we investigated the performance of liquid nitrogen cold trap for purifying a hydrogen stream generated from catalytic and acidic decompositions of NaBH 4 . In the current research, an increase of hydrogen yield is attempted by applying a higher concentration of acidic accelerator and NaBH 4 concentration up to 30 wt% in an aqueous alkaline solution. The paper is arranged in four parts, in which an experimental description, results and discussion and conclusions are presented in the following sections.
Methods
An experimental setup illustrated in Fig. 1 was applied in the experiments. A simple hydrogen generation system was designed to generate hydrogen at a controllable rate and to obtain desired objectives. The main apparatus consisted of fuel solution containers, followed by two peristaltic pumps, a tee connection, product collector and a gas-liquid separator. HCl and NaBH 4 streams made a contact through a Tee connection leading to an instantaneous hydrogen generation along with by-products and excess water. Sometimes, excess HCl was also observed in the product solution. Product solution was collected in the product collector and the hydrogen stream was passed through the gas-liquid separator where the liquid phase was separated and pure hydrogen gas was released from the system. Peristaltic pumps of a single channel driven by AC motor were used (Williamson manufacturing Co., UK), in which a pump of 0.97 ml/min and another of 1.25 ml/min calibrated flow rate or vice versa were applied for feeding NaBH 4 and HCl solutions, respectively. In a later stage, another peristaltic pump of 1.03 ml/min was applied for NaBH 4 solution feeding. Silicone tubing (1.6 mm ID) was used throughout the setup for liquid and gas transportation. Two glass containers of 80 ml were applied as two stages gas-liquid separator. The aim was to purify generated hydrogen stream from moisture and accompanied alkaline mist based on a difference in density. Hydrogen generation rate was calculated using a water displacement method through a 250 ml glass cylinder. Samples of the generated hydrogen after second separation stage were collected using a gas sampler and analysed through a gas chromatography system (Varian CP-3800). Sodium borohydride (98 %) and sodium hydroxide (97 %) purchased from Sigma Aldrich in addition to hydrochloric acid (36 %) from Fisher Scientific were used in the experiments.
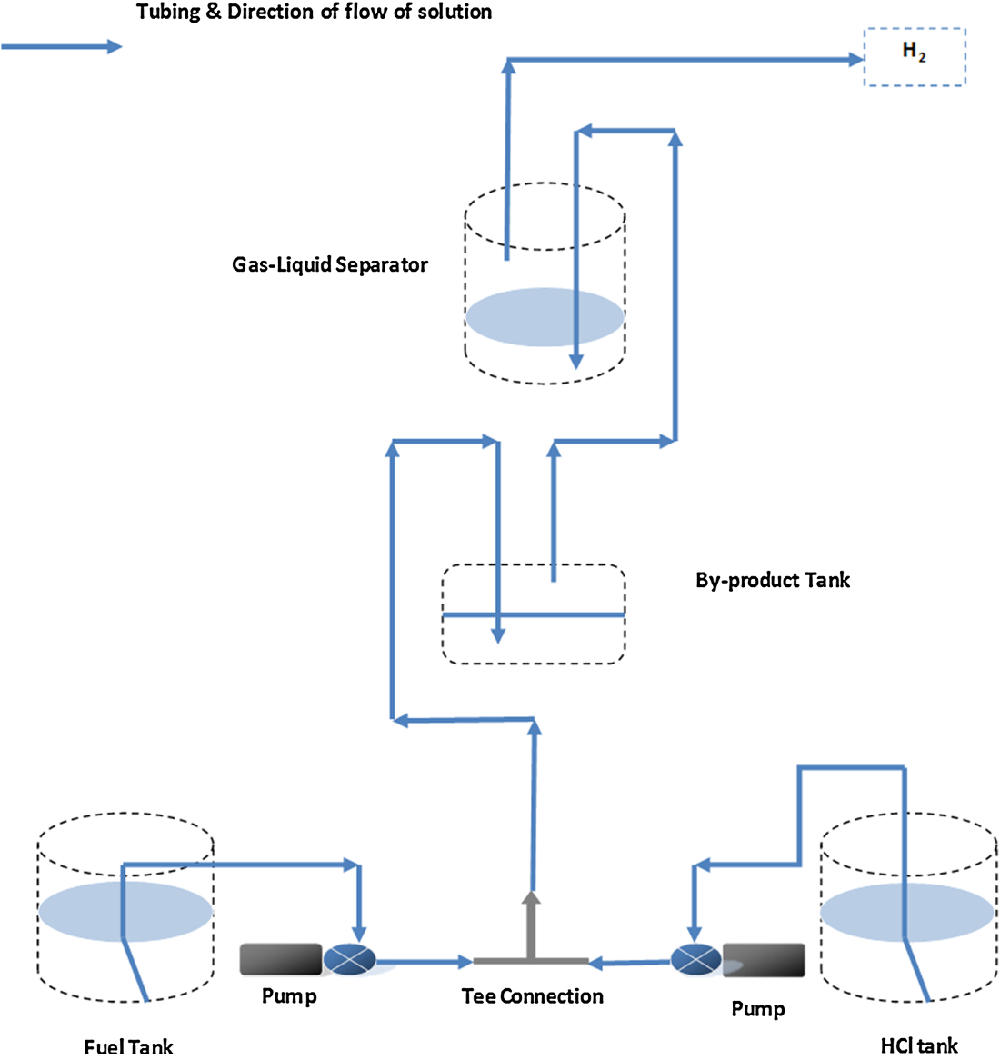
Results And Discussion
Two parallel case studies were conducted in this research. In the first study, use of HCl as an accelerator was investigated and different associated parameters were examined. Second study was devoted to examine feasibility of generating 5.5 wt% of hydrogen that concurs US DOE 2015 storage targets. Samples of experimental results are shown in Tables 1, 2, and 3. A value of 1 wt% NaOH was adopted in all experiments in both studied cases for fuel (NaBH 4 ) solution stabilization, since it has been proven to be optimal concentration [14] .
It is worth noting that a 10-15 wt% NaBH 4 and 1-6 M HCl were indicated in the literature as a workable range for economical hydrogen generation from NaBH 4 catalytic scheme. However, it depends on solutions flow rate and catalyst type. In the current work, a range of fuel solution (NaBH 4 10, 15, 20 and 25 wt%) along with 3 and 4 M of HCl solution were examined in the first case study. These values were selected upon conducting pre-experiments during system pre-commissioning.
A water displacement method was used for measuring generated hydrogen stream rate as it is a pioneer of gas measurement. Measured value was an average of five replicates at 1 min interval between them. The standard deviation of five replicates was \2 in all experiments, which indicates a fair estimation. Figure 2 illustrates these results. Hydrogen density was calculated to be 0.0993 kg m -3 , based on the system operational conditions (fuel solution and acidic solution entering at approximately 20°C and 1.2 barg) and using the ideal gas law.
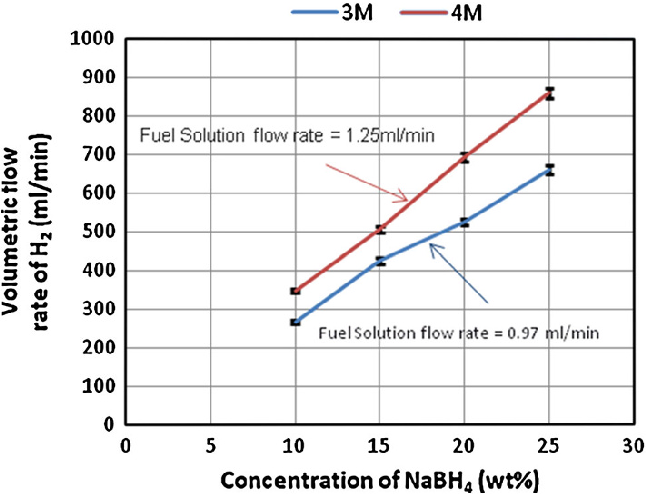
Zali et al. [15] presented the hydrolysis of NaBH 4 in an acidic solution as follows:
Since the acidic hydrolysis is a relatively homogeneous process (due to a controlled contact of two streams) and excess water is available in the bulk, concentrations of water and hydrogen are considered constant. Hence, the kinetic equation of NaBH 4 acidic hydrolysis is presented by the following equation:
The authors [15] reported that a pseudo-first order kinetic model fits the hydrogen generation from NaBH 4 quite well. They concluded that a rate constant (k) of 0.003 s -1 well describes the hydrolysis reaction (acidic scheme) with no catalyst. Accordingly, the activation energy of the acidic hydrolysis can be estimated from Arrhenius equation, considering a rate constant of 0.003 s -1 for a reaction bulk at 20°C (at the contact point of the streams), as follows:
where A is the pre-exponential factor, E a is the activation energy and R is the gas constant. Solving Eq. (5) for E a gives a theoretical value of 10.87 kJ mol -1 for an acidic hydrolysis of NaBH 4 . Comparing this value with the literature shows that it equals one eighth of a value 89 kJ mol -1 for a self-hydrolysis of unbuffered-unstabilized 20 wt% NaBH 4 solution [16] , whereas it approximately equals ten times the value 1.24 kJ mol -1 obtained when applying sulfonated porous carbon catalyst [15] .
It was observed at 3 M HCl that a maximum of 660 ml/ min and a minimum of 267 ml/min H 2 stream rate were obtained from 25 and 10 wt% NaBH 4 , respectively, from applying a fuel solution rate of 0.97 ml/min. However, a significant reduction in the hydrogen generation rate was observed when the molarity of HCl solution was increased to 4 M. After careful investigations, a modification was tried in which the peristaltic pumps were exchanged and consequently a highest hydrogen stream of 860 ml/min from 25 wt% NaBH 4 was obtained at a solution flowrate of 1.25 ml/min. Somehow, researchers concluded that the hydrogen generation rate proportionally increases with an increase of NaBH 4 concentration up to a certain point. After that point, a reduction in the hydrogen generation rate was reported in the work of [9, 14] , and [17] .
In the current study, a continuous increase in the hydrogen generation rate was observed with a parallel increase in NaBH 4 concentration when using acidic scheme and applying HCl as an acid accelerator, as presented in Fig. 2 . This result is partially related to the hydrogen storage capacity which increases theoretically with a parallel increase in NaBH 4 concentration fed to the system. Additional reason could be a high conversion which occurred as a result of an efficient direct contact between fuel solution and acidic accelerator through a tee junction. This result is in agreement with the findings of several researchers [3, 10, 18] . They concluded that using NaBH 4 in a solid form, while being injected through aqueous acidified water, is more efficient than alkaline stabilized form. They showed that an acidic scheme offers to pack more hydrogen per unit volume of hydrogen generator, while the mode of contact between two reacting species would become much easier.
Other important observation was an increase in the hydrogen generation rate upon parallel increases in fuel concentration and feeding rate. This phenomenon has also been observed by Kim et al. [3] up to such extent after which a decrease was denoted in the hydrogen generation rate and interpreted due to a shortage in the contact time with the catalyst. Other researchers Subramanian and Javed [18] and Kim et al. [3] applied controlled injections of fuel solution into the hydrogen generator via syringe and piezoelectric pumps, respectively, and indicated that better hydrogen generation control was achieved. This clearly illustrates that hydrogen production from NaBH 4 using HCl accelerator is highly controllable. Thereby, any desired hydrogen generation rate could be obtained by increasing or decreasing solution flow rates. This identity is so beneficial for onboard fuel cell system applications and ultimately the abovementioned results indicate that a possible amelioration in the hydrogen generation rate could be achieved by applying higher NaBH 4 concentrations and using the proposed scheme as compared with the data reported in the literature obtained via catalytic scheme.
With regards to the acid applied, the literature reported that all acids facilitate an increase in the hydrogen yield with an increase in the acid concentration. Nonetheless, a significant drop was observed with an addition of nitric acid and phosphoric acid as compared to the hydrochloric acid and sulphuric acid. Eventually, three acids were highly recommended with their ideal concentrations which include HCl at 3 N (yield 97 %), H 2 SO 4 at 3 N (96 % yield) and HCOOH at 12 N (87 % yield), [13] . More concise, Demirci et al. [11] specified HCl as an acid of choice for catalysing NaBH 4 hydrolysis with very high hydrogen generation rate. HCl concentrations of 3 and 4 M were applied in the current research. Both of them showed some exceptional results and durability in terms of reaction and by-products generation. However, a clear difference was observed in the reactivity as 3 M solution was quite favourable yet gave maximum conversion efficiency and the reaction was highly controllable. On the other side, 4 M solution showed a strong and vigorous reaction with NaBH 4 which is believed to be due to HCl reactivity. In terms of conversion efficiency and hydrogen generation rate, HCl stream of 4 M concentration was found less competitive even after pumps exchanged. Accordingly, 3 M of HCl is found to be an optimal concentration in case of low NaBH 4 concentration, whilst 4 M concentration is recommended for high NaBH 4 concentration. The efficiency of hydrogen generation was calculated according to the following formula:
where; V actual = the actual hydrogen volume measured via water displacement method.
V theoretical = volume of hydrogen estimated theoretically according to Eq. (2), where 4 mol of hydrogen is generated from decomposing 1 mol of NaBH 4 .
Conversion efficiency is a vital parameter behind successful generation of hydrogen gas. This efficiency shows the amount of fuel which is totally converted into its byproducts during specific time duration. In this study, a maximum and a minimum conversion efficiency of fuel solution was obtained as 99 and 98 % from applying 3 and 4 M HCl solutions, respectively.
The application of two stages gas liquid separator (GLS) in the current system has proved useful in terms of accomplishing high conversion, where any unspent fuel (not converted in the tee junction) is forcefully converted in the product collector, 1st GLS, and results in liberating rest of hydrogen gas. Eventually, NaBH 4 fuel was fully converted into by-products after few minutes of reaction completion. Ultimately, 2nd GLS accomplished the removal of any hydrolysed mist coming with the generated hydrogen stream, which was mainly due to a high reaction temperature.
The estimated hydrogen generation efficiency through the experiments of first case study is shown in Fig. 3 .
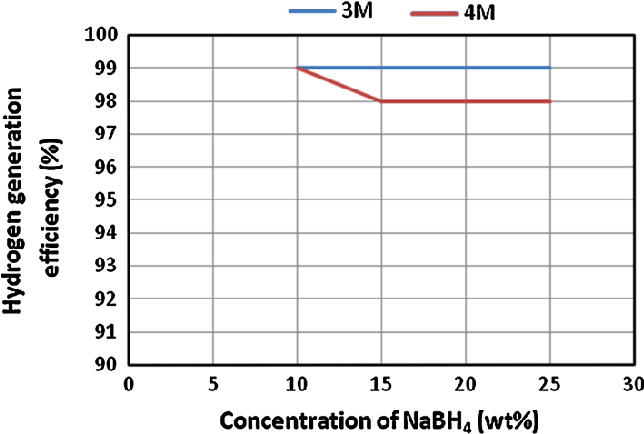
By applying the proposed experimental configuration, a hydrogen gas stream of higher flow rates was generated with a maximum conversion efficiency of NaBH 4 .
It should be noted that the reaction temperature is a vital parameter that affects the reaction rate and generation efficiency. Retnamma et al. [16] reported that the reaction rate increases with both temperature and initial NaBH 4 concentration for a fixed NaBH 4 conversion and decreases with increase in NaBH 4 conversion for a fixed temperature and initial NaBH 4 concentration for a self NaBH 4 hydrolysis process. The temperature effect was also investigated by many researchers in which a positive effect was indicated when increasing the solution temperature for the catalytic hydrolysis of NaBH 4 . In the current work, the efforts were dedicated to apply the acidic hydrolysis at ambient temperature to adopt the system for mobile fuel cells. Hence, the contact between fuel solution and the HCl stream was conducted via a tee junction at ambient temperature (&20°C), whereas the product solution was directed to a GLS. An increase in the aqueous product temperature (collected in the GLS) was observed, where the temperature was measured in the range (305-328 K); Tables 1, 2 , and 3, for several case studies applied in this research. The product temperature has increased with an increase in both NaBH 4 and HCl concentration in the system. The recorded data indicated a reasonable increase in the temperature which can be treated easily for mobile fuel cell applications.
A power analysis was conducted based on the determined hydrogen flow rate. It is known that 2 mol of electrons (equivalent to 12.04 9 10 23 electrons) is released at the anode for each mole of hydrogen entering a polymer electrolyte membrane (PEM) fuel cell, according to the following formula.
Since 1 A is equivalent to 6.25 9 10 18 electrons per second, therefore 0.5 9 10 -5 mol/s or 3 9 10 -4 mol/min of hydrogen is required for each ampere generated in PEM fuel cell. Accordingly, the power of PEM working at 700 mV can be estimated as follows [19] :
It was observed that in addition to the hydrogen generation rate, the power output was also increased when increasing NaBH 4 concentration. Highest power output was estimated to be 74 W/min with 860 ml/min of hydrogen flow rate when applying 25 wt% of NaBH 4 fuel solution. Lowest power output of 24 W/min with hydrogen flow rate of 268 ml/min was estimated when applying 10 wt% of NaBH 4 fuel solution. Figure 4 illustrates the increase in the estimated power with an increase of NaBH 4 concentration at 3 and 4 M HCl.
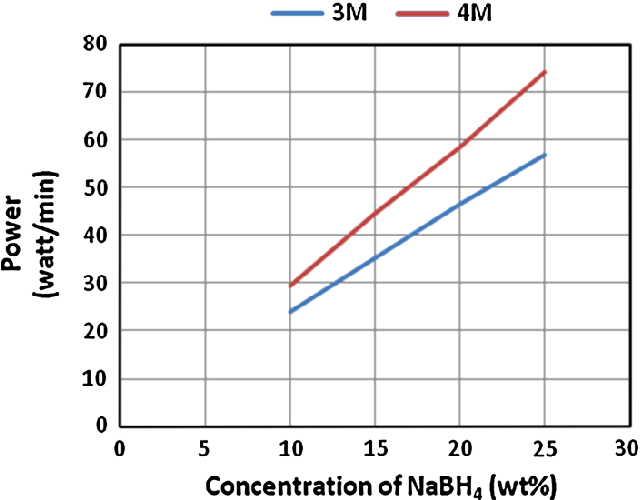
Purity of the generated hydrogen stream was checked upon analysing several samples, collected from the outlet of 2nd GLS using a gas sampler, applying GC method. Figure 5 shows analysis results of one collected sample. Oxygen and nitrogen peaks can be observed at low intensity and attributed to penetration of air into gas sampler during sample collection.
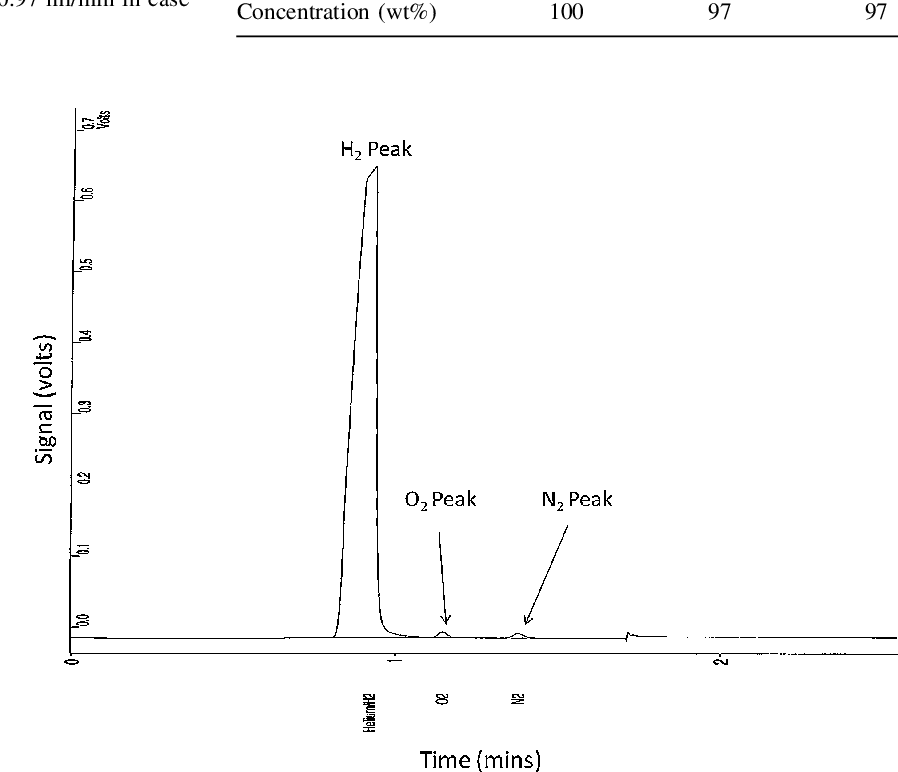
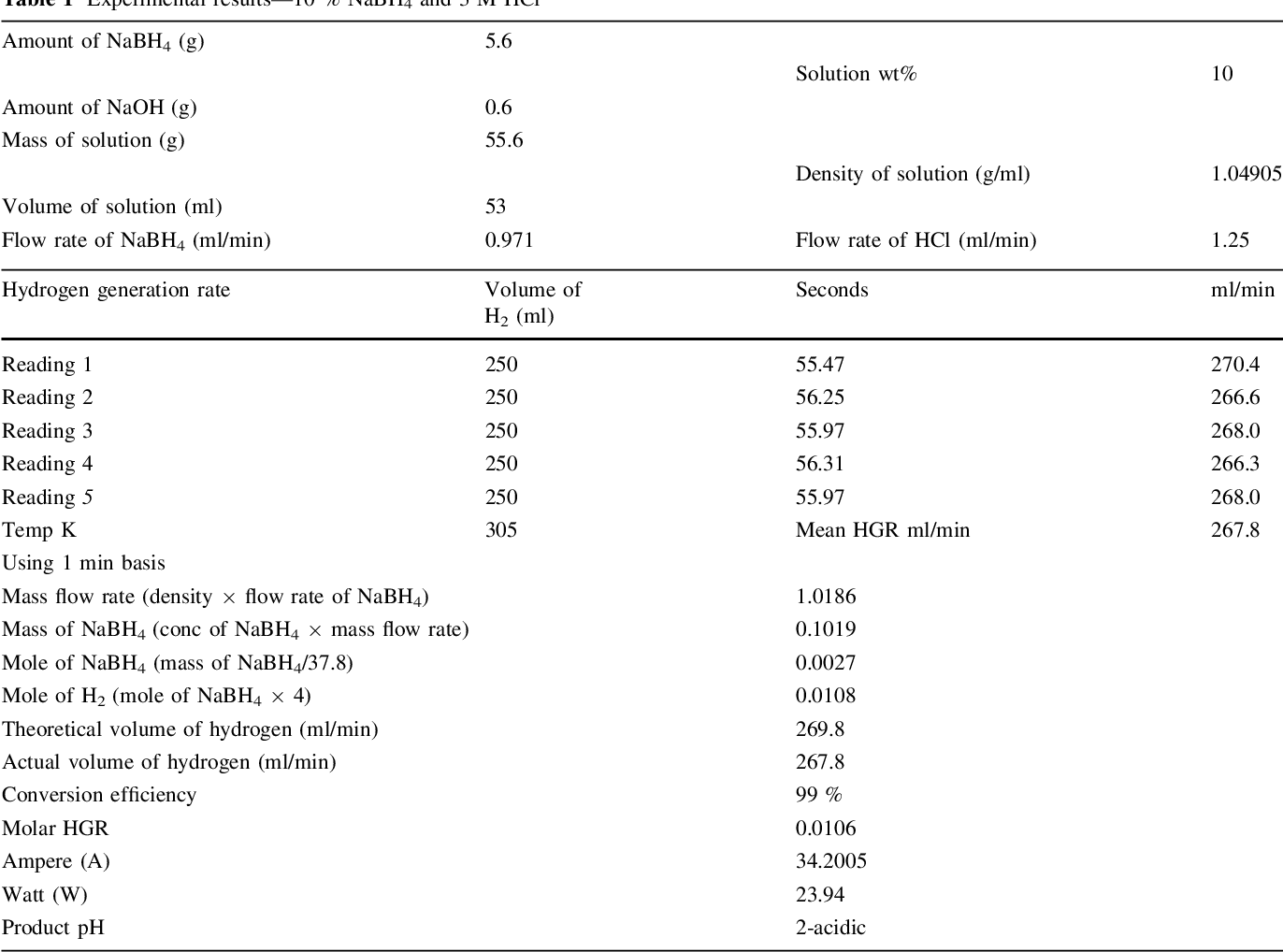
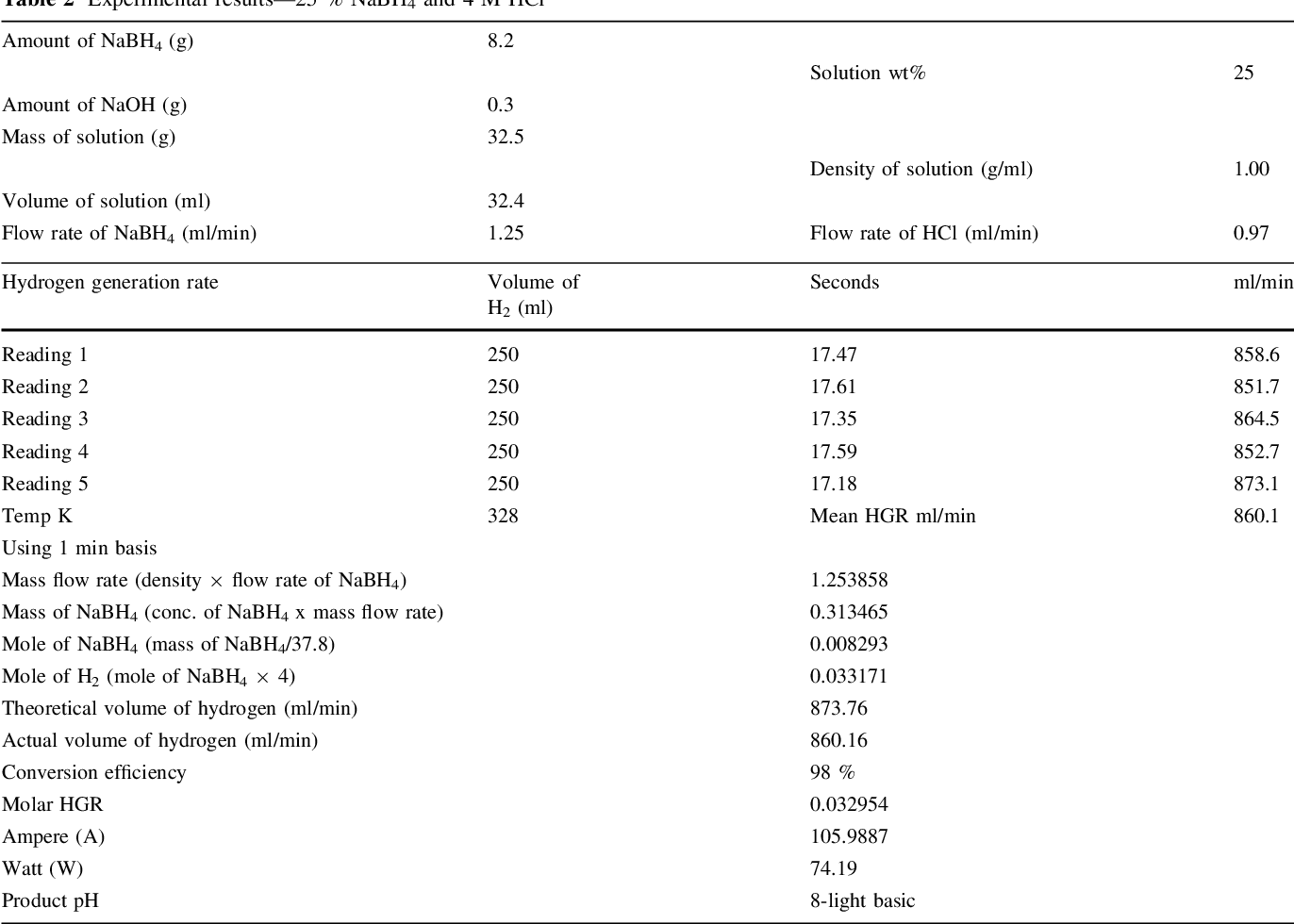

GC analysis results are shown in Table 4 , where 97 wt% was produced from two samples injection, and indicates a high convergence to the data estimated from previous analysis based on applying a water displacement method.
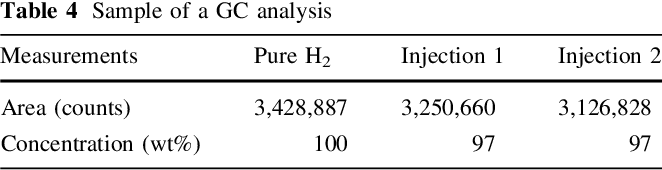
As it was essential to verify system performance at higher NaBH 4 , a 30 wt% NaBH 4 was injected to the system in the second case study. The selection of this concentration was to meet the US DOE targets for 2015 for onboard hydrogen storage capacity which equals 5.5 wt% gravimetrically. Gervasio et al. [20] reported that a 100 % conversion efficiency was accomplished from 30 wt% of NaBH 4 through a catalytic scheme using Ru catalyst. The exceptional result achieved might be related to different reasons such as excess amount of catalysts used in their reactor, which is not practical for vehicular fuel cell system application.
Although a higher generation efficiency was achieved ([99 %) when 30 wt% of NaBH 4 was applied using the same conditions of the first case study, an appearance of precipitated materials (crystals of sodium borates) in the collector (1st GLS) was observed. These precipitated materials also appeared when a lower NaBH 4 , up to 25 wt%, was used but with very low quantity. Therefore, several parameters were explored aiming to reduce crystals formation and their precipitation. Ultimately, NaBH 4 fuel solution injection rate was found to be the main reason; accordingly, a new peristaltic pump of 1.03 ml/min (calibrated flow rate) was applied instead. In consequence, the hydrogen generation efficiency was reduced to 98 % but still concurs the 2015 target, and the precipitation was stopped. It can be observed that the estimated hydrogen flow rate (863 ml/min) generated from applying 30 % NaBH 4 concentration at 1.03 ml/min fuel solution and 3 M HCl was equivalent to a rate (860 ml/min) generated from applying 25 % NaBH 4 at 1.25 ml/min and 3 M HCl, which means that 74 W/min (4.44 kWh) is produced from both cases. However, use of lower flow rate of fuel solution is indeed more economical at large-scale systems and also advantageous in terms of lowering liberated heat and by-products crystallization and precipitation.
Conclusions
Two case studies were conducted to investigate feasibility of using HCl scheme as an alternative to a catalytic scheme for hydrogen generation from sodium borohydride system serving vehicular fuel cells. The main objective was to meet the DOE 2015 onboard hydrogen storage target (5.5 wt%). Exceptional results showed that onboard mixing of fuel and acidic streams in the proposed system of two gas-liquid separators proved useful for higher conversion efficiency and system performance. 98 % conversion efficiency without any sodium borates precipitation was achievable upon optimizing NaBH 4 fuel solution flow rate. Hence, a hydrogen generation rate of 863 ml/min was obtained from applying 30 wt% NaBH 4 at 1.03 ml/min and 3 M HCl at 0.97 ml/min, achieving 4.44 kWh of power. Other important feature observed was reaction controllability, where it can be stopped by addition of alkaline medium (e.g. sodium hydroxide) or accelerated by adding acid.
Open Access This article is distributed under the terms of the Creative Commons Attribution License which permits any use, distribution, and reproduction in any medium, provided the original author(s) and the source are credited.