HCI meets Material Science: A Literature Review of Morphing Materials for the Design of Shape-Changing Interfaces
Authors
- Isabel P. S. Qamar
- Rainer Groh
- David Holman
- Anne Roudaut
Table of Contents
- Abstract
- Introduction
- Review Of Shape-Changing Mechanisms
- Stretchable Structures
- Elastomers
- Elastomers Within Hci
- Auxetic Materials
- Auxetic Materials Within Hci
- Deployable Structures
- Rollable Structures
- Rollable Structures Within Hci
- Foldable Structures
- Foldable Structures Within Hci
- Inflatable Structures
- Inflatable Structures Within Hci
- Variable Stiffness Materials
- Anisotropic Structures
- Anisotropic Structures Within Hci
- Multi-Stable Structures
- Multi-Stable Structures Within Hci
- Shape Memory Materials
- Shape Memory Alloys
- Shape Memory Alloys Within Hci
- Shape Memory Polymers
- Shape Memory Polymers Within Hci
- Bridging The Gap
- Conclusion
- References
License
Abstract
With the proliferation of flexible displays and the advances in smart materials, it is now possible to create interactive devices that are not only flexible but can reconfigure into any shape on demand. Several Human Computer Interaction (HCI) and robotics researchers have started designing, prototyping and evaluating shape-changing devices, realising, however, that this vision still requires many engineering challenges to be addressed. On the material science front, we need breakthroughs in stable and accessible materials to create novel, proof-of-concept devices. On the interactive devices side, we require a deeper appreciation for the material properties and an understanding of how exploiting material properties can provide affordances that unleash the human interactive potential. While these challenges are interesting for the respective research fields, we believe that the true power of shape-changing devices can be magnified by bringing together these communities. In this paper we therefore present a review of advances made in shape-changing materials and discuss their applications within an HCI context.
Introduction
Current consumer devices, such as laptops, smartphones and wearable devices, often have form factors that are determined by their use of flat, planar display technology. In recent years, the availability of thin-film flexible displays and smart materials has enabled HCI researchers to actively explore organic [88] , morphing [148, 198] and more expressive interactive forms. From interactive spherical displays [16] to mobile Permission to make digital or hard copies of all or part of this work for personal or classroom use is granted without fee provided that copies are not made or distributed for profit or commercial advantage and that copies bear this notice and the full citation on the first page. Copyrights for components of this work owned by others than ACM must be honored. Abstracting with credit is permitted. To copy otherwise, or republish, to post on servers or to redistribute to lists, requires prior specific permission and/or a fee. Request permissions from permissions@acm.org. phones that bend to notify a user of an incoming call [75] , and to pneumatic interfaces that expand to become exoskeletons or couches [202] , there are many recent examples of shaped interface design in the literature (see [191] for an overview).
From a design perspective, this transition from flat to shaped interfaces is more complex than simply readjusting current practices. The introduction of shape blends the boundary between interaction and industrial design [87] , and requires a next-generation designer to conceptualise interaction in an object's form. This change puts a greater need for HCI practitioners to learn about and adapt the advances made in material science and to quickly apply them towards shaped devices.
The maturation of 3D printing and its influence on prototyping [152] , and the emergence of thin-film displays and their relationship to bendable interfaces [110] , are testament to the fact that the advances in material science can have a direct impact on HCI research. In this paper, we discuss how the evolving relationship between HCI and material science can be framed, and why synergies between the two fields are critical for the design of shape-changing devices. As a first step, we contribute a review of developments in shape-changing material science to establish a baseline literacy and to make recent work from material science available to the HCI community.
Within this review we make a systematic exploration of recent developments in material science, focusing on the technologies applicable to the context of shape-changing devices, including stretchable structures, deployable systems, variable stiffness materials and shape memory materials and discuss their potential application for morphing interactive devices, with the aim of building a bridge between material science and HCI. Examples are provided from the broad HCI literature where these technologies have already been implemented. Finally, we discuss the challenges in bridging the gap and propose a way forward. Our contribution is a road map for designers who want to learn more about the advances in material science and use them for the design of shape-changing interfaces.
Review Of Shape-Changing Mechanisms
In this section we present a review of the outputs from material science that could enable morphing capabilities for shapechanging devices. Thill et al. [236] present a review of shapechanging concepts for aircraft morphing skins. This work is comprehensive and highly cited in its field. We have therefore used the shape-changing categories from this paper that we consider to be most applicable to HCI; namely stretchable structures, deployable structures, variable stiffness materials and shape memory materials. We then discuss how the different technologies within these categories could be applied within the HCI community. Table 1 contains the key material science references within this paper and summarises outputs from HCI with respect to each shape-changing mechanism.
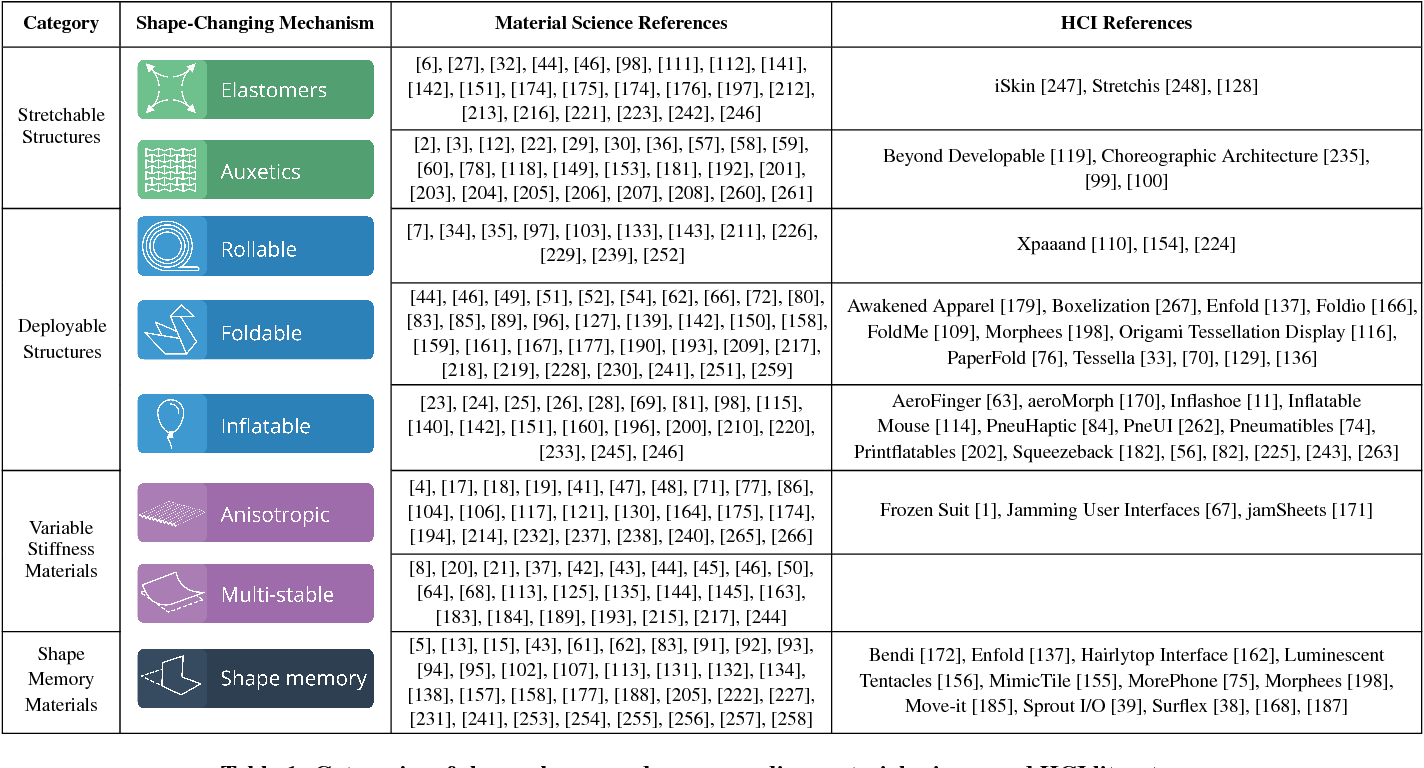
Several review papers have been published that define the different types of shape-change and their applications. Organic User Interfaces (OUIs) describes how computer interfacesno longer limited to rigid flat surfaces-can exhibit shape, deformation and non-planar forms [88] . Rasmussen et al. [191] present a review of existing work on shape-changing interfaces and identify eight different types of deformation. Roudaut et al. [198] propose the term shape-resolution that extends the definition of display resolution to shape-changing interfaces. It is based on the model of Non-Uniform Rational B-splines (NURBS) and has ten features to characterise shapechange mathematically. Coelho et al. [40] adopted a more technology driven approach with their taxonomy describing the technological properties of shape-changing devices. Examples include power requirements, the ability to memorise new shapes and input stimulus, such as voltage potential, or the ability to sense deformations. In this paper, rather than focusing on shape-change from an HCI perspective, we review current state-of-the-art morphing technologies that have been developed to meet desirable shape-change within engineering industries (e.g. aerospace). We also discuss how these technologies may be harnessed by HCI researchers for the development of shape-changing interactive devices.
Stretchable Structures
Stretchable structures are the basis of shape-changing devices that require large changes in surface area and rely on a material/structure that is compliant enough to allow for large-scale deformation. In this section, two classes of stretchable structures are discussed: elastomers and auxetic materials.
Elastomers
Elastomers, such as silicone, are a type of polymer that have historically been used in seals and adhesives, gloves, tyres, toy balloons, rubber bands, in shock absorbers and in moulded flexible parts. These materials are typically safe in their end form, widely available and are relatively easily manipulated by the user. Their main advantage is their low elastic modulus (i.e. the resistance of a material to being stretched, also known as Young's Modulus) which enables them to easily deform (i.e. strain) up to 1000% of their original length [32, 236] , resulting in large achievable changes in topology. Due to their weak intermolecular structure, elastomers can stretch easily without large forces and return to their original shape when the force is removed, thus exhibiting a shape-memory effect [107] .
Depending on their molecular structure, elastomers fall into one of two categories: thermoset (such as silicone rubber) or thermoplastic. Whilst thermoset elastomers are typically stronger, thermoplastics are melt-processable and easily recycled, lending themselves to manufacturing processes such as 3D printing [223] . The properties of these materials display non-linear behaviour, meaning that different shape-changing responses may be achieved depending on how quickly the material is stretched and on the surrounding temperature [27] , indicating the need for tightly controlled user conditions to ensure repeatability and minimal degradation of the material. The glass transition temperature (T g ) is a particularly important characteristic of polymers and is the temperature region at which a polymer transitions from a brittle, glassy state to a soft, rubbery state [27] . Elastomers, therefore, must be used at a temperature well above their T g point in order to exhibit the desired characteristics for shape-change.
In recent years, elastomers have been developed for new applications including artificial muscles [6, 176] , soft robotics [141, 216, 242, 246] and stretchable electronics [111, 112, 212, 213] . Silicone has frequently been used in the development of pneumatically actuated soft robots due its durability and the ability to fabricate internal chambers that can be inflated and deflated to enable specific deformation patterns from a single pressure source [98, 142, 151] . Advances in stretchable electronics have been reviewed in [197] , and the authors suggested that these technologies show promising potential for several HCI applications including sensory skins for robotics, structural health monitors and wearable communication devices.
Elastomers Within Hci
Although many instances of stretchable structures within the HCI community have been reported using fabrics [146, 173, 195, 199] , few studies have employed elastomers alone. Polydimethylsiloxane (PDMS), a silicone-based organic polymer, served as the base material of iSkin [247] and Stretchis [248] and enabled the development of stretchable user interfaces for sensing and display. A significant drawback of elastomers, particularly for shape-change, is the trade-off between stretchability and strength. Typically, a material that is able to undergo large increases in surface area has low strength (therefore not particularly robust) and vice versa [221] , which has likely prevented their use in larger scale prototypes by HCI researchers without being coupled with another component. However, elastomeric polymers show particular promise for achieving high resolution shape-change due to their highly deformable nature. Some of these materials are costly and require complex knowledge of polymer processing (which has potentially been an inhibitor in their adoption in shape-changing research). Nonetheless, many are still easily accessible to HCI researchers and do not require any specific skills or equipment other than the ability to mix together two components in a specified ratio.
Auxetic Materials
Auxetics are materials that exhibit a negative Poisson's ratio (v); in other words, they become wider when stretched and narrower when compressed. Their performance relies on the spatial arrangement of their internal architecture rather than their material composition. The internal structure of these materials typically consists of an arrangement of connected hinge-like cells that have a re-entrant geometry (i.e. the angles of the honeycomb cells point inwards), causing the sides to expand outwards when stretched (Figure 1 ) [31, 236] . Typically, auxetic structures are anisotropic (i.e. different properties in different directions), undergoing different expansion rates depending on the axis stretched, however, this deformation is Stretchable Structures [6] , [27] , [32] , [44] , [46] , [98] , [111] , [112] , [141] , [142] , [151] , [174] , [175] , [174] , [176] , [197] , [212] , [213] , [216] , [221] , [223] , [242] , [246] iSkin [247] , Stretchis [248] , [128] [2], [3] , [12] , [22] , [29] , [30] , [36] , [57] , [58] , [59] , [60] , [78] , [118] , [149] , [153] , [181] , [192] , [201] , [203] , [204] , [205] , [206] , [207] , [208] , [260] , [261] Beyond Developable [119] , Choreographic Architecture [235] , [99] , [100] Deployable Structures [7] , [34] , [35] , [97] , [103] , [133] , [143] , [211] , [226] , [229] , [239] , [252] Xpaaand [110] , [154] , [224] [44], [46] , [49] , [51] , [52] , [54] , [62] , [66] , [72] , [80] , [83] , [85] , [89] , [96] , [127] , [139] , [142] , [150] , [158] , [159] , [161] , [167] , [177] , [190] , [193] , [209] , [217] , [218] , [219] , [228] , [230] , [241] , [251] , [259] Awakened Apparel [179] , Boxelization [267] , Enfold [137] , Foldio [166] , FoldMe [109] , Morphees [198] , Origami Tessellation Display [116] , PaperFold [76] , Tessella [33] , [70] , [129] , [136] [23], [24] , [25] , [26] , [28] , [69] , [81] , [98] , [115] , [140] , [142] , [151] , [160] , [196] , [200] , [210] , [220] , [233] , [245] , [246] AeroFinger [63] , aeroMorph [170] , Inflashoe [11], Inflatable Mouse [114] , PneuHaptic [84] , PneUI [262] , Pneumatibles [74] , Printflatables [202] , Squeezeback [182] , [56] , [82] , [225] , [243] , [263] Variable Stiffness Materials [4] , [17] , [18] , [19] , [41] , [47] , [48] , [71] , [77] , [86] , [104] , [106] , [117] , [121] , [130] , [164] , [175] , [174] , [194] , [214] , [232] , [237] , [238] , [240] , [265] , [266] Frozen Suit [1] , Jamming User Interfaces [67] , jamSheets [171] [8], [20] , [21] , [37] , [42] , [43] , [44] , [45] , [46] , [50] , [64] , [68] , [113] , [125] , [135] , [144] , [145] , [163] , [183] , [184] , [189] , [193] , [215] , [217] , [244] Shape Memory Materials [5] , [13] , [15] , [43] , [61] , [62] , [83] , [91] , [92] , [93] , [94] , [95] , [102] , [107] , [113] , [131] , [132] , [134] , [138] , [157] , [158] , [177] , [188] , [205] , [222] , [227] , [231] , [241] , [253] , [254] , [255] , [256] , [257] , [258] Bendi [172] , Enfold [137] , Hairlytop Interface [162] , Luminescent Tentacles [156], MimicTile [155] , MorePhone [75] , Morphees [198] , Move-it [185] , Sprout I/O [39] , Surflex [38] , [168] , [187] independent of their length scale [149] . Although many studies have investigated auxetic properties in 2D, this behaviour can also be observed in 3D using a similar topology [58, 260] .
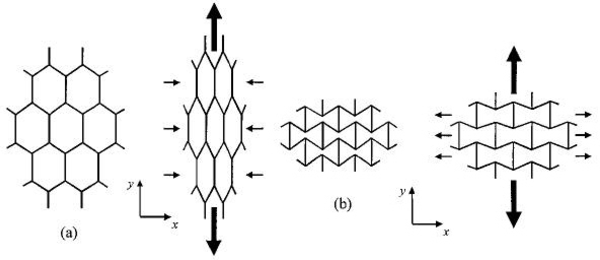
Auxetic materials have been synthesised as foams [29, 30, 204, 207] , ceramics [126] , composites [36, 60] , crystals [12, 79, 264] and polymers [3, 22, 181, 192] , with re-entrant honeycomb cellular structures being the most extensively researched to date [149, 206, 208, 261] . The hexagonal lattice shown in Figure 1 is perhaps the simplest form of an auxetic cellular arrangement, however, other tessellating geometries, such as chiral [2] and rotating unit [78, 90] , are also capable of creating an auxetic shape-changing mechanism. Further attempts have been made to develop smart auxetic structures from shape memory alloys (SMAs), in order to introduce some multifunctional capability such as actuated shape-change [205] . An interesting characteristic of auxetics for shape-change is that these structures display synclastic curvature when bent. In other words, unlike non-auxetic structures which form a saddle shape when bent (Figure 2a) , auxetic materials form a domeshape devoid of any crimps (Figure 2b ), making them suitable for designing and building structures with complex curvatures and shapes [57, 203] . In [119] the authors exploited this characteristic to physically realise complex surfaces such as shoes, sculptures, face masks and clothing via auxetic linkages by introducing cuts into the material so that the elements formed could rotate relative to each other in an auxetic manner.
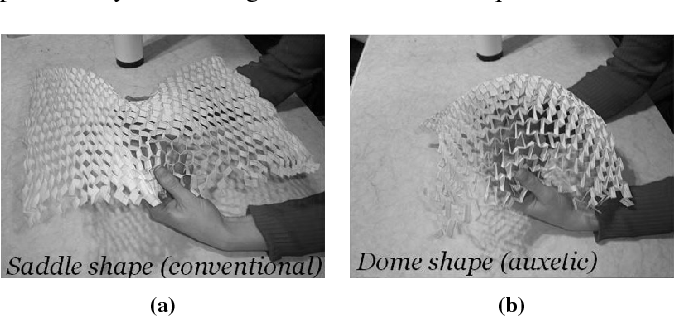
Auxetic Materials Within Hci
Auxetic materials display many advantageous properties, particularly for shape-changing applications, such as the ability to achieve large changes in surface area, a high resistance to fracture (i.e. robustness) and high energy absorption [78, 261] . However, their widespread use has largely been limited by the complex procedures to generate these materials using traditional manufacturing methods. With recent advances in 3D printing, the potential exists to more readily fabricate cellular designs to introduce shape-changing functionality, particularly in the case of 3D re-entrant structures [118, 149, 153, 260] . For example, Theodoros et al. [235] 3D printed an auxetic structure that could be pneumatically actuated to achieve a change in curvature, and in [99] the authors 3D printed a metamaterial door latch from a single block of NinjaFlex (a flexible TPU filament) that enabled rotary movement of the handle to be transformed into linear motion of the latch. Although the modelling of the precise deformation of these structures may be complex, the lack of awareness of auxetics as a means for shape-change is likely to be the main reason for the scarcity in HCI literature. Yet, with the developments in 3D printing and extensive literature detailing auxetic designs, these structures are now more accessible to the HCI community as there is no longer a need for expensive equipment or materials. Auxetic materials therefore show promising potential for shape-change, particularly when a degree of curvature is required.
Deployable Structures
Deployable shape-changing mechanisms enable structures and devices to be stowed for transport or easy handling and expanded when required. In the case of shape-changing devices this may also enable a change in function of the device depending on the current configuration. In this section, three classes of deployable shape-changing mechanisms are discussed: rollable, foldable and inflatable.
Rollable Structures
Examples of rollable mechanisms found in everyday use include roller blinds, garage shutters and for efficient storage of fabrics and other flexible materials. A large proportion of research on rollable structures to date has focused on space applications [239] , most notably for in-space deployment of lightweight solar sails with minimal packing volume during launch. Rollable carbon-fibre reinforced polymer (CFRP) booms were developed by DLR for an Earth-orbiting Solar Power Satellite (SPS) [211] that consisted of two laminated sheets in an Ω-shape bonded together to form a tubular structure. Flattening this shape made it easier to bend in one direction, enabling the booms to be coiled for storage [226] . Araromi et al. [7] created a microsatellite gripper that utilises a pre-stretched, rollable dielectric elastomer membrane bonded to a flexible but inextensible frame that remains rolled-up until the pre-stretch is released during deployment. Another advantage of some rolled, deployable devices such as a carpenter's tape, is that they can automatically uncoil and then snap into a stable uncoiled configuration that is load-bearing [180] .
An exciting prospect for rollable structures is in the development of flexible electronics, with advances in thin, flexible display technology enabling the concept of rollable displays to be explored [143] . This is perhaps the application of rollable structures that has been of most interest within HCI to date. Several studies have focused on developing the technology, including [34, 97, 143, 229, 252] . Typically metal foils, ultrathin glasses and plastic films are considered ideal materials for the flexible substrate, with rollable polymer films showing particular promise due to their flexibility, low cost and excellent optical clarity, in addition to being amenable to a wide range of manufacturing processes such as roll-to-roll processing and inkjet printing [103] . However, they tend to suffer from a high coefficient of thermal expansion (CTE), i.e. there is a large change in the material size with changes in temperature, which can make integration with display layers a challenge [35] .
Rollable Structures Within Hci
Several studies investigate the user interaction with rollable devices and explore the physical modes of interaction [110, 154, 224] . However, the authors all noted that despite recent developments in flexible displays, the components required to realise such devices are still unavailable and the focus of their studies landed primarily on the interaction with the rolling mechanisms rather than the display technology itself. Furthermore, the flexible nature of the inorganic thin films used in electronic devices tends to promote brittle failure [133] , highlighting that the challenges in utilising rolling structures for shape-changing interfaces lie not only with HCI researchers, but also with material scientists and the need for further developments in the materials technology.
Foldable Structures
The high strength-to-weight ratio of folded objects enables the development of thin, lightweight, hollow, shape-changeable geometries that can be easily deployed into 3D and flattened into 2D for storage and transport [166] . In recent years, engineers have looked to the ancient Japanese tradition of origami to inspire the evolution of engineering structures that can be fabricated, assembled, stored and morphed in unique ways [72, 177] . The applications of foldable structures are widespread and have been implemented in an array of practical scenarios including in the design and deployment of solar sails [211] and space telescopes [55, 249] , in sandwich panel cores [66, 85] , in the folding of sheet metal [53] , in packaging and containers [52, 251] , in robotics [62, 89, 127, 167] , biomedical devices [65, 122, 190] and electronics [80, 96, 161, 218, 228, 259] .
In origami mathematics, a fold is regarded as an ideal surface having zero-thickness where any deformation of the surface does not result in stretching, contraction or self-intersection. The location of these folds are known as creases and they, in addition to the direction, magnitude and sequences of folding, determine the shape of the structure [49, 177] . When implementing origami to create physical structures, the surface no longer maintains zero-thickness and the magnitude of a fold is described by the folding angle and the radius of curvature at the fold line. To generate these folds, one of two approaches must be taken; local bending of the material or the use of a hinge. The latter concept is referred to as rigid origami, where the facets and crease lines are replaced with panels and hinges, and is particularly relevant for large shape-changing structures that require a high degree of stiffness [230] .
For certain applications, such as in remote locations, at very small or large length scales, or where packaging is complex and requires automation, the capability of these structures to self-fold becomes essential. The active folding of structures has been reported using shape memory materials [241] , polymer swelling [101] and magnetic fields [62] , and an extensive review of self-folding mechanisms for both hinge and bending type folds using active materials are reported in [177] . For example, in [83] the authors developed a self-folding sheet consisting of triangular tiles of glass-fibre impregnated with resin, that uses SMAs attached to the upper and lower surfaces to enable actuation. To address the issue of sheet thickness, an elastomer is used for the joints and a series of magnets enable folding into any polyhedral shape (Figure 3) . Felton et al. [62] presented self-folding shape-memory composites made from two outer layers of prestretched polystyrene (a shape-memory polymer (SMP)), two layers of paper and a printed circuit board (PCB) made from polyimide and copper. When heated, the SMP contracts causing the composite to fold. SMPs have also been used to create a number of different self-folding composite shapes; from boxes to Miura-ori patterns [241] . The folding and unfolding of structures becomes increasingly complex with increasing number of folds due to the expanding number of folded possibilities [139] . A well-known example of origami folding that was initially created to efficiently pack and deploy solar panels for space missions is the Miura-ori tessellated folding pattern [150] . This herringbone pattern consists of a series of convex mountain and concave valley creases that enables the entire structure to be folded or unfolded simultaneously, avoiding the complexity of folding sequences [219] . Schenk et al. [209] formed folded cellular structures by stacking individual Miura-ori sheets that were bonded along the joining fold lines, in which the folding kinematics were preserved. By varying the unit cell geometry within each layer, the authors developed a self-locking, folded cellular structure, where the motion could be halted in a predetermined configuration. Adopting this idea into shape-changing devices may enable its mechanical functionality to be altered on demand.
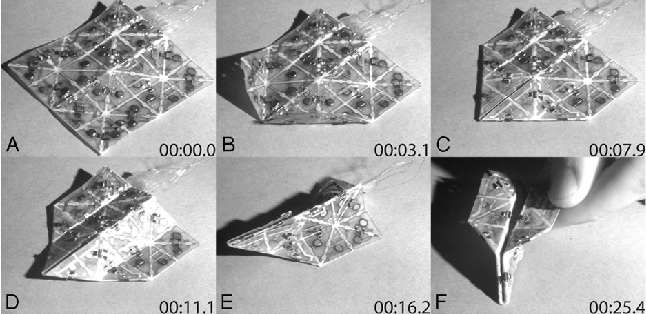
In addition to folding, kirigami also permits cutting to obtain 3D shapes from 2D sheets, enabling not only changes in shape, but also large changes in volume with highly tailorable properties in each axis [159] . Neville et al. [159] detailed the manufacturing process of honeycomb kirigami structures that involves a sequence of cutting, corrugating and folding. Although they used Polyetheretherketone (PEEK) to demonstrate their design, the authors suggested that this method could be applied to any material, provided that it can be cut and folded. They showed that a series of threaded cables was a simple method of deforming the structure (Figure 4 ), but smart materials such as SMPs could also be used for actuation [158] . Dias et al. [51] also demonstrated that mechanical actuators can be designed that enable roll, pitch, yaw and lift, by tuning the arrangement and location of cuts within thin elastic sheets.
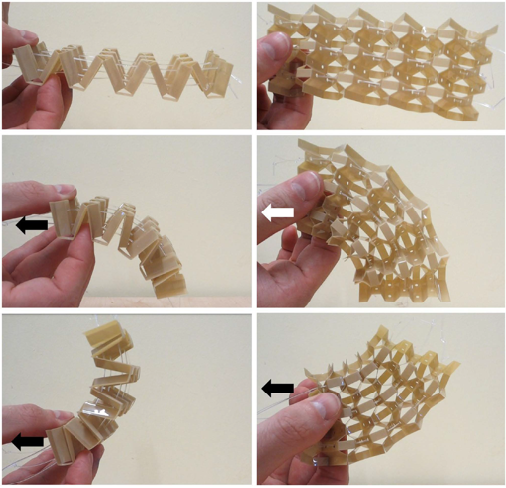
Foldable Structures Within Hci
Many instances of origami folding can be found within HCI, such as within fashion and textiles to create shape-changing skirts [179] and jackets [137] , and in the development of interactive objects [33] . Origami mechanisms have also been used to create interactive folding displays [76, 109, 129] and input devices [70, 116] . For example, Olberding et al. [166] introduced Foldio, a fabrication technique for Foldable Interactive Objects, i.e. folded sheets of paper, plastic or cardboard, that can sense user input such as touch and deformation, and display output and actuated shape change through printed electronics. They demonstrated this technology through a series of applications including interactive packaging and furnishing, paper prototyping, custom-shape input and output devices, such as a game controller, and a shape-changing display.
The broad literature available shows that foldable structures are not a new concept in HCI, particularly with regards to origami-inspired devices. The basics of folding are easy to implement, reproducible and the shape-changing mechanism can be achieved with almost any compliant material. However, they require an external structure to guide them into shape and as a result, the speed and maximum displacement of the shapechange is highly linked to the actuation method [177] . Another limitation is that these structures are considered membrane materials, i.e. to enable better foldability, a high bending stiffness must be avoided, leading to a compromise in structural performance (strength and stiffness) as the structures can only take load in tension and not in compression [53, 54] . Such trade-offs are likely to impact the characteristics of the device, but we expect to see more innovative solutions as we move towards higher fidelity developments and gain an improved understanding of the kinematics of folding. By cutting as well as folding (kirigami), it may be possible to create devices that can achieve large changes in volume as well as surface area.
Inflatable Structures
An inflatable is a structure that can be inflated with gas, normally air, helium, hydrogen or nitrogen. Their popularity is largely due to their low weight and ability to pack into small volumes, conforming to almost any shape that can be deployed when required. Other advantages include their low production cost, high strength due to the large surface area over which they are able to absorb loads, and high reliability of deployment [28] . As a result, they have found their way into many applications including vehicle wheels, furniture, inflatable boats and buoyancy systems [81] , airbags [23, 233] , membrane roofs [9, 105, 165] , soft robotics [151, 160, 196, 245, 246] , medical treatments [10, 14, 147, 234] and for entertainment.
Extensive research has also been conducted in the use of inflatables for space-based devices [69] . For example, small UAVs that can be tightly packed for ease of transportation or launching and that have significant robustness to withstand impact on landing, are of interest for military operations. This includes vehicles that are inflated on site and hand-launched, those which are gun-launched and inflate in flight, and ejectable (one-time use) or retractable (reusable) systems [25] . Schenk et al. [210] highlighted that efficient packing schemes are necessary to ensure reliable deployment of inflatables.
The choice of material for an inflatable largely depends on the application. Everyday balloons tend to be made from latex rubber, polychloroprene or nylon, due to their low cost and ease of manufacture, and have often been adopted by HCI researchers in prototype development. Inflatable structures for space tend to consist of a combination of more costly, high strength-to-weight, durable fabrics such as Kevlar ® and Vectran ™ (a high-strength, liquid crystal polymer) with a polyimide (Kapton ® ) or polyurethane membrane material that acts as a sealant [220] . Car airbags are typically formed from thin woven nylon or polyester fabric [108] , while polyethylene is often found in cushioning and packaging. Silicone has also been widely used in medicine [123] and in soft robotics for artificial muscles [115, 140] . Ultimately, the strength and stiffness of the inflatable structure is controlled by the internal pressure and the elastic modulus of the restraint material [26] .
Inflation pressure provides structural rigidity by placing tension in the walls of the structure. Therefore, to maintain the inflated shape, the internal pressure must equal or exceed any external pressure that is applied to the structure. The larger the structure, the lower the inflation pressure that is generally required. After a period of time, the inflation gas will inevitably escape through imperfections in the inflatable skin that may have occurred through manufacture, folding or deployment, reducing the overall shape and stiffness. Furthermore, inflated structures that lack reinforcement are more susceptible to puncture [210] . As a result, the concept of rigidisable materials, i.e. "materials that are initially flexible to facilitate inflation or deployment and become rigid when exposed to an external influence", has been introduced by Cadogan et al. [24] , with an extensive review of the different methods given in [210] .
Inflatable Structures Within Hci
An advantage of inflatable structures within HCI research is that they can be deflated, partially inflated or fully inflated, enabling a wide range of stiffness properties or actuation forces to be achieved. This has attracted computer scientists in recent years to adopt these structures for wearable technologies and to provide interactive haptic feedback to users. Examples include interactive shoes that adapt to different surfaces or to the user's foot morphology [11] , therapeutic cushions that can adjust according to the user [263] , and in inflatable pads fitted to car steering wheels that can pulsate and alert drivers to potential problems without utilising their vision or auditory senses that may already be fully engaged [56] .
Inflatable materials have also found their way into interactive input and display devices including an inflatable mouse [114] , inflatable buttons and controls [82, 243] , and in an inflatable multi-touch display surface that could dynamically deform from a flat, circular display to a convex or concave, hemispherical display according to the context of the user's task [225] . This highlights that inflatable structures for shape-change have already been well adopted within HCI as, for example, balloons are very easy to obtain at low cost and require little to no expertise or equipment. However, challenges often exist in ensuring reliable and predictable deployment and sufficient structural robustness after deployment, potentially limiting their use in more demanding environments [200, 210] . By incorporating more robust materials or combining membrane materials with durable fabrics, in a similar manner to the aerospace or automotive industries, prototype development may be accelerated closer towards its end-use.
Variable Stiffness Materials
In this section, we discuss how shape-change can be achieved by designing a structure so that the stiffness properties vary in different directions, focusing on two mechanisms in particular: anisotropy and multi-stability.
Anisotropic Structures
Anisotropy, as opposed to isotropy, refers to the directional dependance of material properties. By designing an object such that the stiffness varies along different axes, it can be deformed in a direction with minimum actuation force [236] . The tailoring of stiffness is not a new idea. Bone, for example, has different elastic properties in two orthogonally opposed directions (known as orthotropic); parallel to and normal to the long axis of the structure [19] . Wood is an orthotropic structure as it has different properties in three perpendicular directions; axial, radial, and circumferential, due to its grainlike structure [77] . In contrast, metals and glass are isotropic and have the same macroscale properties in all directions.
Examples of stiffness tailoring for shape-change can largely be found in the development of morphing technology for aircraft [121, 237] , such as bend-twist coupling of beams for gust alleviation [71] , and in wind turbine blades [47, 124] . In fibrereinforced composites, anisotropy is introduced through the distribution of material through-thickness and through fibre orientation [121] . By reducing stiffness in the chord direction and increasing in the span direction, researchers have aimed to create morphing aircraft skins that have sufficient stiffness to withstand aerodynamic loads, yet are flexible enough for actuation [238] . For example, Peel et al. [175] developed a manufacturing process for fibre-reinforced elastomeric composites using an elastomer matrix, such as urethane or silicone, with glass fibre reinforcement, and showed notable variation in the resulting elastic modulus in different directions [174] .
Although in material science, anisotropy is typically linked to the material's microstructure, it may also be introduced via its structure, such as through corrugation, which is perhaps more accessible to HCI research than high cost composites. Corrugated structures have long been found in the packaging industry (e.g. cardboard) [4, 17, 18] , in civil infrastructures (e.g. in roofs, walls and pipes), [104, 240] , in aerospace structures (e.g. the Junkers Ju-52 of the 1930's) [106, 232, 265, 266] and in sandwich panels for marine and aerospace applications [48, 86, 117, 194] . This is due to their high strength-to-weight ratio, energy absorption capabilities and anisotropic behaviour, which can be attributed to the high degree of stiffness transverse to the corrugation direction, in comparison to along the corrugation direction. By specifying the dimensions and materials of both the face sheets and corrugated core, a range of structural characteristics for morphing can be achieved [266] . For example, Norman et al. [164] explored the use of curved corrugated shells for structural morphing and determined that, although there is a loss in membrane (i.e. in-plane) stiffness, the sheets are capable of large changes in Gaussian curvature ( Figure 5 ). Bi-directional cores have also been developed to modify the stiffness in both directions [130, 214] .
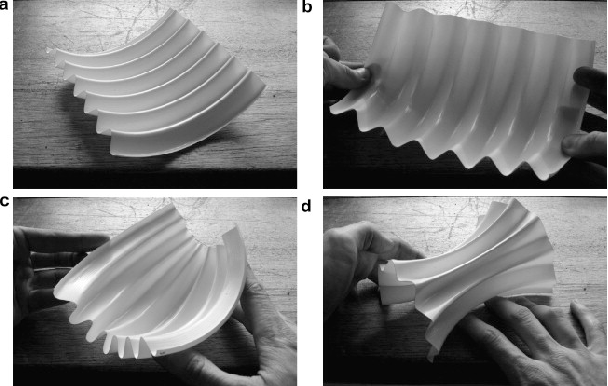
Anisotropic Structures Within Hci
The concept of material anisotropy for shape-change has been investigated to some extent by HCI researchers by using particle jamming to achieve variable stiffness properties, such as in [1, 67] , where the authors focused on alternating between soft and hard deformability. However, Ou et al. [171] showed that it was also possible to introduce anisotropic deformation using jamming through the structural design of the jammable materials, such as by weaving multiple jamming units into the material, using interleaving flaps in the elastic air bladder, or by introducing crease patterns or cutting geometrical patterns into the jamming flaps [169] . They envisioned that by incorporating more complex weaving patterns or increasing the resolution, it may be possible to program more sophisticated deformation interactions such as the direction of stretching, degree of rolling, bending angle and shear deformation.
The developments in 3D printing have also made shape-change via anisotropy more accessible. Due to the layer-by-layer deposition, 3D printing is inherently anisotropic, resulting in objects that are much stronger in the horizontal printing direction than the vertical direction [186] . Typically, this is an unwanted characteristic, particularly for brittle materials, however, this has enabled the printing of hydrogel architectures with localised, anisotropic swelling behaviour that can result in complex, three-dimensional shape-change when immersed in water [73] . As in the case of auxetics, 3D printing has also encouraged cellular materials to be designed that can exhibit different deformation characteristics in different axis [41] .
One of the main challenges in implementing anisotropy is that this type of shape-change, such as that exhibited in morphing aircraft wings and wind turbine blades, tends to be very subtle and may not be suitable for achieving large, nonlinear changes in shape that can be accomplished using deployable structures, elastomers and multi-stable structures [236] .
Multi-Stable Structures
Multi-stable structures undergo large, rapid deformations between multiple stable mechanical shapes. The Venus flytrap is a well-known bi-stable structure that snaps from an open to closed state when small hairs on the plant are triggered by potential prey [68] . Another example is the slap bracelet that consists of layered, flexible, bistable spring bands sealed within a fabric, silicone or plastic cover. By straightening out the bracelet, tension is applied to the springs which is released when slapped against the wearer's arm, causing the bands to spring back and wrap around the wrist [120] . Self-retracting tape measures also undergo large rapid deformations between different states. During manufacture, a concavo-convex crosssection is introduced through heat treatment that gives the tape longitudinal structural rigidity when deployed and enables rapid retraction when bent [180] . Harnessing such characteristics may enable HCI researchers to achieve rapid actuation between multiple device shapes.
Extensive research into multi-stability has been conducted within composite materials [50, 125, 144, 145, 183, 184] . The snap-through phenomenon occurs when a structure is forced to transition from one equilibrium, which is stable under small perturbations, to another (usually by an external force), by transitioning through a region of instability. This region of instability, or negative stiffness, means that significant deformation is required to move between the two stable states and explains why bistability is so attractive for morphing applica-tions [8, 45] . The snapping of thin composite laminates occurs due to residual stresses that are generated during the cure cycle of an asymmetric lay-up (due to a mismatch in CTE of the constituent layers) or as a result of initial curvature. The tristability of composite shells has also been reported in [37, 244] . Typically, only low actuation forces are required to generate large deformations in multi-stable composites. Various actuation mechanisms to provide this 'snap-through' shape-change for morphing applications have been investigated, including piezoelectric ceramic-based actuators [20] , shape memory alloys [43, 113] and thermal patches [135] , and a comparison between them was made in [21] . A passively adaptive structure that does not rely on external mechanisms for actuation was also reported in [8] . In [163] the authors developed multistable corrugated panels from a Copper-Beryllium alloy and suggested that these structures could potentially be used as a mount for flexible displays or deployable electronic devices.
Shan et al. [215] demonstrated the accessibility of fabricating bistable structures by 3D printing multi-stable, architected materials. When compressed, the internal beam elements move into another stable state but with higher energy, exhibiting local, bistable deformation. The beams can then return to their initial configuration when a sufficient reverse force is applied, enabling multiple changes in shape. In [189] the authors created a bistable metamaterial that moves through several metastable states via snap-through buckling when stretched, until it reaches full extension, achieving strains of up to 150%.
Multi-stability has also be combined with deployable shapechange such as folding. The Buckliball [217] is a good example of this and is a continuum silicone shell structure developed by Shim et al. that undergoes a structural transformation when the internal pressure is reduced. A pattern of circular voids exists on the shell so that when the internal pressure falls below a critical value, the narrow pieces of material between the voids collapse inwards causing buckling of the ball. In [193] the author discusses in more detail how buckling of slender structures can be exploited to develop functional mechanisms for smart morphable surfaces. As another example, Daynes et al. [44] developed a bistable, elastomeric origami morphing structure, made from silicone, with locally reinforced regions of acrylonitrile butadiene styrene (ABS). The structure could deploy from a flat to textured arrangement ( Figure 6 ), under pneumatic actuation, and maintain its shape without sustained actuation. They highlighted that this cellular structure is a lightweight, inexpensive method of creating an actuating, shape-changing mechanism due to the low cost of materials and the use of 3D printing to fabricate the mould. However, the authors noted that the more compliant the structure is, the less able it is to support high external forces [46] .
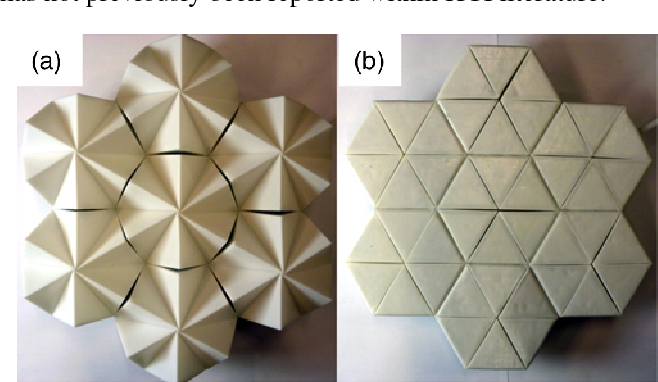
Multi-Stable Structures Within Hci
In HCI we are used to computers reacting at a fast rate but in shape-changing interfaces this requirement is more difficult to fulfil as some shape-changing mechanisms, such as SMAs and SMPs, have slow actuation times that may affect the user experience [231, 255] . In contrast, bistable materials typically have actuation times of a few milliseconds [21] . Although multistability is normally associated with composite materials, we have shown that this type of shape-change can be exploited using simple and inexpensive materials and methods. The main challenge of implementing multi-stability within HCI is that these structures are typically binary, i.e. they are limited to two stable shape configurations (bistable), and the shapechange is challenging to control [42] . As multi-stability is a non-linear phenomenon, it is often not intuitive how additional stable configurations can be achieved by tailoring the underlying mechanics. Furthermore, the greater the number of stable configurations, the harder it is to control the actuation dynamics due to possible nonlinear interactions between modes [64] . Consideration must also be made as to how these structures will be actuated. Nonetheless, multi-stability may provide a mechanism to achieve rapid actuation and shape-change that has not previously been reported within HCI literature.
Shape Memory Materials
Shape memory materials are a class of material that exhibit a shape memory effect (SME) due to their ability to change stiffness as a result of an externally applied stimuli. Here we discuss the two most common forms of shape memory materials: shape memory alloys (SMAs) and shape memory polymers (SMPs).
Shape Memory Alloys
The shape-changing mechanism behind SMAs is based on a reversible martensitic transformation. When the SMA is cooled it undergoes a martensitic transformation from its austenite phase to its twinned martensite phase, at which point the material is malleable and may be reconfigured into the desired shape (a deformed temporary martensite phase). When heated above the austenite finish temperature the material undergoes a reversible martensitic transformation, returning to its original, rigid shape in the austenite phase. This is known as a one-way SME. It is also worth noting that SMAs exhibit a temperature hysteresis ( Figure 7) . In other words, the temperature required for the martensite to austenite transformation is higher than for the austenite to martensite transformation [236] .
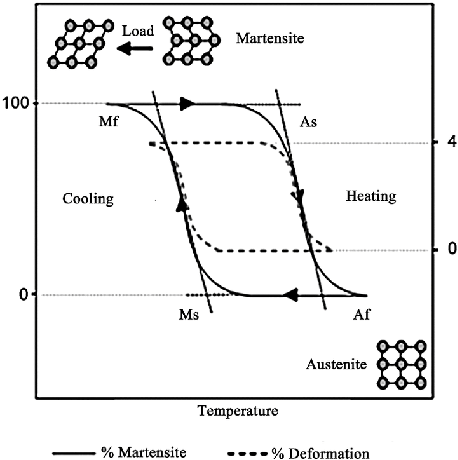
Materials with a two-way SME are able to remember their shape at both low and high temperatures and switch between them. To achieve this, the material must be subjected to repeated one-way SME cycles [134] . These training requirements, in addition to the limits in maximum recoverable strain and the tendency of the shape recovery to deteriorate at high temperature over time, means that one-way SMEs are generally favourable due to their greater reliability [227] . A third characteristic of SMAs is pseudoelasticity. This means that the SMA can transform between the austenite and martensite phase without a change in temperature when a mechanical force is applied [102] .
To date, SMAs have been developed into many shapes including solid (such as wires), film and even foam. Commercially available SMAs are typically based on one of three alloys: NiTi-based (Nitinol), Cu-based and Fe-based, the choice depending on the application. For example, NiTi SMAs exhibit very high performance, are highly reliable and have frequently been implemented in the development of HCI prototypes. Febased alloys have excellent biocompatibility and are often found in biomedical applications. Cu-based alloys are low cost but relatively weak and are generally only used for one-time actuation [227] . All these materials are thermo-responsive, therefore relying on heat to trigger the SME, however, recent advances have also been made in developing magnetoresponsive SMAs based on ferromagnetic materials [94] .
Shape Memory Alloys Within Hci
The most useful applications of SMAs within HCI are as an actuating mechanism for shape-change. SMAs have several advantages over motors, pneumatics and hydraulic systems such as low cost, reduced size and complexity, their ability to react directly to environmental stimuli such as temperature, their biocompatibility and low weight [157] . Furthermore, they are capable of actuating in 3D, thereby enabling the evolution of structures and devices that can extend, bend and twist [102] . They have also been widely adopted within HCI prototypes. For example, SMAs have been used to animate paper [185, 187] , to create novel, deformable user interfaces and displays [75, 155, 172, 198] and in the development of shape-changing and texturally-rich surfaces [38, 39, 168] .
Although SMAs have been widely used within HCI research, they are not suitable for every application. They have a relatively small usable strain and are not easy to control. They have a low actuation frequency, low accuracy, are not very energy efficient and have a demanding training regime [102] . In addition, rapid heating of SMAs is challenging and although this can be achieved by Joule heating (i.e. applying an electrical current), care has to be taken not to overheat and damage the elements or harm the user [61, 188] . Furthermore, the cooling process is also slow, highlighting the relatively slow actuation response time of SMAs, which is also influenced by the size and shape of the SMA (i.e. larger and thicker SMAs take longer to heat and cool) [5, 231] . This is likely to have a significant impact on the user experience and it may be necessary to look to alternative mechanisms, such as multi-stability, to achieve rapid actuation between different shape states.
Shape Memory Polymers
SMPs also exhibit an SME and have several advantages over SMAs. They are lighter, lower in cost (both in the raw material and processing), easier to process into almost any shape and their material properties can be more readily manipulated [256, 257] . Furthermore, SMPs have a greater recoverable strain (up to 1100%) than SMAs and the shape memory process can be triggered by a wide range of stimuli including UV [131] , moisture [258] , heat [138] or several stimuli combined [95] .
The SME observed in SMPs is largely due to their molecular structure and the processing and programming conditions. Examples include segmented polyurethane, styrene-based polymers and crosslinked polyethylene [92] . These polymers undergo a transformation to a more deformable state when heated above their transition temperature, which may be its T g (see elastomers) or its melting temperature. On cooling, the polymer hardens into the deformed shape and maintains this shape even when the force is removed. If the polymer is heated back above its transition temperature, it will undergo a shape memory recovery process and return to its programmed shape [236] . This is unlike SMAs where the stiffness is reduced when the temperature is lowered. Due to the wide shape recovery temperature range of SMPs, it is possible to have more than one memorised shape, achieved either by triggering different stimuli or through multiple transitions within different temperature ranges [13, 15, 254] . In depth reviews into the developments of SMPs can be found in [91, 92, 138] .
Shape Memory Polymers Within Hci
Both within the HCI and materials communities, SMAs have been more widely utilised than SMPs for actuating shapechange. The lack of understanding in the behaviour of SMPs, particularly regarding their long-term use, means that few are commercially available and as a result, they have not been widely implemented [227] . Like SMAs, the actuation response of these materials is relatively slow [255] . However, the field has seen recent growth and researchers have begun investigating their potential use in a wide variety of applications including self-tightening sutures [132] , biodegradable stents [250] , surface patterning (e.g. braille) [93] , morphing wings [107, 178] , deployable structures [222] and self-healing materials [253] , due to their highly tailorable structure.
Bridging The Gap
As seen in Table 1 , some shape-changing technologies have been more widely adopted within HCI than others. For example, foldable and inflatable structures and SMAs have been used in a variety of applications, ranging from interactive displays and input/output devices to clothes and furniture. However, little research has been conducted using rollable and multi-stable structures to enact shape-change within HCI. We argue that this can be attributed to two key factors: (1) a lack of awareness and understanding of shape-changing technologies and their material characteristics by HCI researchers, and (2) a lack of availability of equipment, materials and lab space for HCI researchers to support their work. SMAs, for example, are readily available online and require limited expertise. In contrast, the complex mathematics behind auxetic materials can make their fabrication challenging. Multi-stability and anisotropy have not been widely adopted within HCI, potentially due to an absence in appreciation of these mechanisms and the methods required to implement them. These are also relatively new fields in material science and work is still required by the materials community to mature the technology.
Although material science, like HCI, is multi-disciplinary and benefits from collaboration between physicists, chemists and engineers, the approaches to research also have some key differences. For example, manufacturability is a key consideration in the design and development phases in material science and projects often go through many development cycles (years, or even decades) before they are physically realised. In contrast, HCI researchers often develop proof of concept prototypes in much shorter time frames, with attention being paid to the expressivity and ease of appropriation of the technology. This difference in requirements and approach to research is perhaps another key factor in the gap between these two fields.
The choice of shape-changing mechanism is also largely dependant on factors such as performance (e.g. strength and robustness), power consumption, actuation capabilities (e.g. maximum displacement and speed) and shape-change resolution (e.g. granularity, curvature, strength and speed), and this review highlights that the different technologies vary in each of these criteria. Stretchable and deployable structures tend to be limited to applications that do not require significant strength or robustness, however, they are able to achieve a higher number of shape configurations and larger changes in area and/or volume. Variable stiffness materials are capable of more robust shape-change that can be used for more demanding applications, however, the number of shape configurations and degree of shape-change tends to be limited.
Actuation speed and power consumption also differ between each of the technologies. For example, SMAs have a slow response time, are only capable of providing a low actuation force and require a high power consumption, however, many shape configurations can be achieved. In contrast, multi-stable structures deform at a rapid rate and require little force to do so, however, they are limited in the number of stable mechanical shapes they can morph into. Each of these criteria are essential to both material science and HCI applications, highlighting how these fields can benefit from working together.
To improve the synergy between these two fields and to foster future collaboration, we propose the following way forward:
• The creation of a language and/or common syntax between the fields to address the gap in understanding terminologies and methods. This paper provides a starting point for addressing this issue by defining material properties that HCI researchers may be unfamiliar with.
• The creation of online platforms where researchers within HCI can express what is needed in terms of hardware manufacturing, as well as share current developments. As a first step in this direction we placed the content of this paper at www.morphui.com and will update it regularly.
• The creation of software design tools to increase the accessibility of material outputs that do not require an in depth understanding of the science behind such developments. Ideally this would enable HCI researchers to have a platform which provides them with an awareness of the behaviour and characteristics of these materials/mechanisms.
• The creation of hardware design tools to enable the use of printers, Fab Labs etc., for reproducing material science outputs in a more accessible manner.
The capabilities of layering and arranging material, brought on by the additive manufacturing (3D printing) revolution, has sparked interest in compliant, shape-adaptive and multifunctional systems in both HCI and material science. The first-hand experience of writing this review suggests that the HCI community may benefit from a broader awareness of state-of-the-art material systems, whereas the material science community has little experience in embedding information processing, i.e. "intelligence", into structures. Perhaps, the greatest means of fostering synergies between these two fields is taking the leap and interacting with colleagues across discipline boundaries just for curiosity's sake.
Conclusion
With the aim of accelerating the design of shape-changing devices, we have provided a review of the advances in material science from an HCI perspective. We see this approach as a road map for next generation designers that want to better understand material science and adopt shape-changing mechanisms in their work. We also believe that creating OUIs requires a redefinition of the tools we use during the design process. The tools needed for shaped-interface design need to be more expressive, like the raw and versatile materials an industrial designer might use to create complex geometries. A change like this can happen if HCI practitioners are attentive to shape-change developments from a material science perspective. This work is a step in this direction as it bridges a gap between material science, HCI and shape-change.